
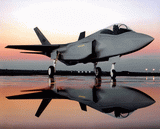
The $200
billion concept: Lockheed’s X-35 Joint Strike Fighter.

|
Fighter
Jet Contract a Proving Ground for IT
Design, production
present key challenges
By DAN
VERTON
(November
12, 2001) 
Lockheed Martin's
capture of the Pentagon's $200 billion Joint Strike Fighter (JSF) contract may be the most
complex and demanding test of product data management software in the defense and
aerospace industry, experts and analysts said.
In winning the largest defense contract in
history on Nov. 2, Bethesda, Md.-based Lockheed Martin Corp., which is partnering with Los
Angeles-based Northrop Grumman Corp. and U.K.-based BAE Systems, defeated the team led by
Chicago-based The Boeing Co. And although IT played a critical role in Lockheed's ability
to produce a winning concept for the advanced jet fighter, the upcoming design and
production phases will be the real test of how well Lockheed's software team performs,
said experts.
"When you firm up a design, that's when you firm up your costs and the
manufacturer's process capability and ability to produce," said Mike Burkett, an
analyst at AMR Research Inc. in Boston. It's in the design phase that "you find out
if your concept actually works," he said.
The Pentagon will scrutinize Lockheed's performance during the upcoming design phase
and as production of the estimated 3,000 jets ramps up in 2009, said Burkett. The rollout,
which will include the U.K. and other U.S. allies, will continue for 25 years.
Schedule and cost control, which are highly dependent on the use of collaboration
software, will be critical to Lockheed keeping the contract, Burkett noted. There's also a
remote chance that the company could drop the ball and lose the contract, he said.
Lockheed officials couldn't be reached for comment.
Responsibility for keeping the program on track rests on the software that
helped Lockheed snag the contract in the first place. Metaphase from Structural Dynamics
Research Corp. (SDRC) in Milford, Ohio, could eventually support up to 50,000 users in 30
countries once the JSF program hits full speed, said Tim Nichols, manager of Aerospace
& Defense Industry Marketing at SDRC, now a part of Electronic Data Systems Corp. in
Plano, Texas.
"When it goes full course, it's going to be the most complex virtual enterprise
ever conceived," said Nichols. "These aircraft change every five years as
technology changes. So tracking changes and reuse is absolutely critical."
Everybody - from the design team to suppliers - needs to have access to the most recent
data, 3-D models and drawings, said Erica Rugullies, an analyst at Giga Information Group
Inc. in Cambridge, Mass. "Without a PDM (product data management) tool, they would be
printing out a paper copy of a 3-D drawing, and a trading partner would be forced to
re-create it," said Rugullies.
The Lockheed and Boeing JSF development teams both used Windchill Web-based portal
software from Needham, Mass.-based Parametric Technology Corp. to integrate multiple PDM,
enterprise resource planning and database systems during the initial concept phase of the
contract, which included the production of three prototype aircraft from each team.
The design phase ahead will be one of the biggest challenges Parametric's software has
ever encountered and will undoubtedly become a model for other industries, said Mike
Brown, senior vice president of sales for aerospace and defense at Parametric.
"Whether it's the aerospace, high-tech or automotive industry, you really have the
same kind of business issues that you're grappling with," he said. |